Making Ikat
On this page...
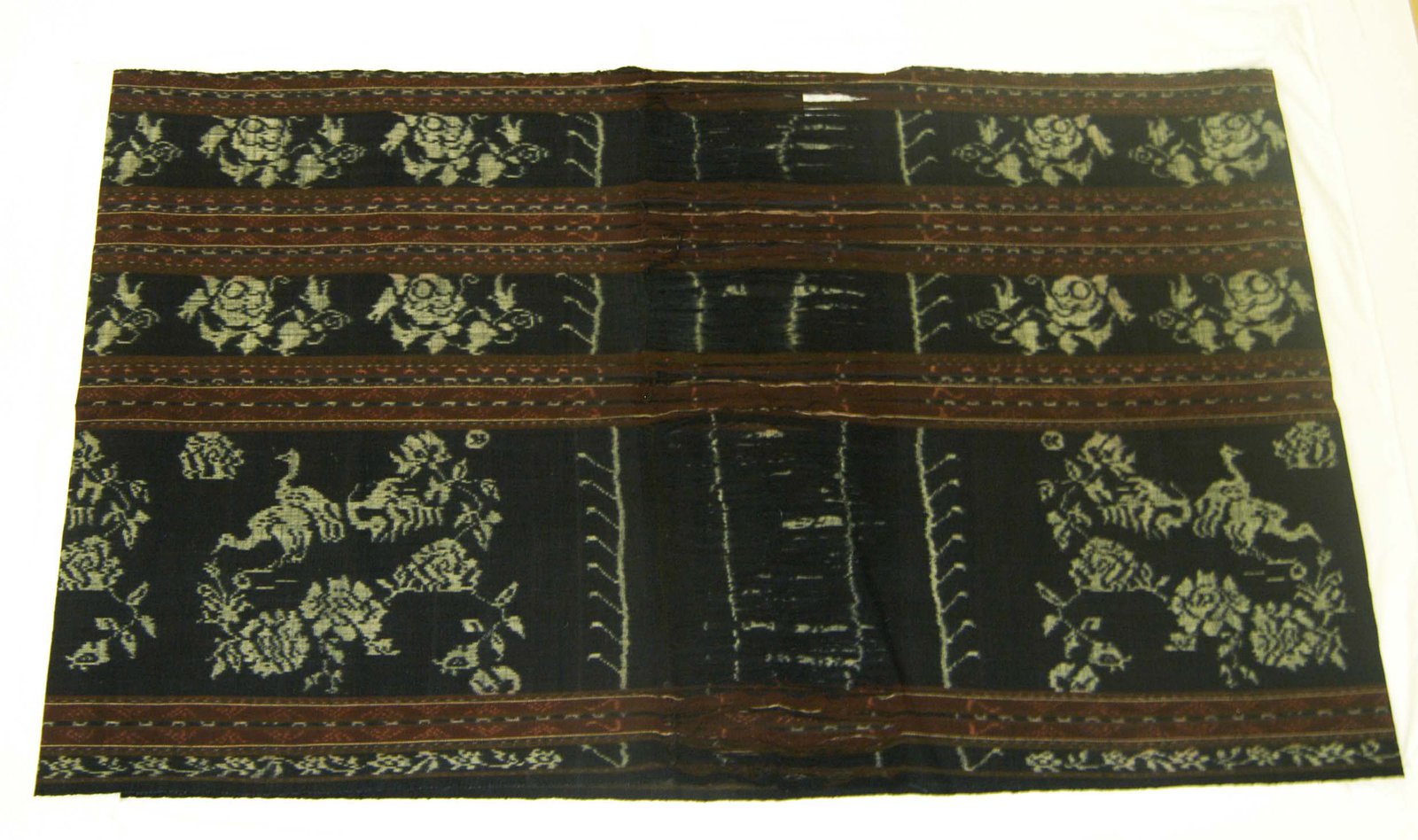
© Australian Museum
Ikat is a traditional hand-woven cloth not unique to, but commonly associated with, Indonesia where some of the finest examples were and still are produced. The word ikat, meaning to ‘tie’ or ‘bind’ in the Indonesian language, alludes to the process of production, for its essence is a ‘resist’ dying of yarn before weaving. The cloth pattern is preconceived and made by selectively tying bundles of thread that are tinted in liquid dye. Different sections of the thread are tinted in chosen dye (such as red, yellow, green, white, and maroon), so the process of tying and dying is laboriously repeated until all desired colours are in place. At this stage the future pattern of the cloth is already arranged. The coloured thread is placed on a loom in preconceived length and width, and the weaving brings a pattern of thread into the two-dimensional design of fabric. Typically, such design is fuzzy as a result of the difficulty aligning each length of tread with perfect precision through weaving. Highly skilled artisans with extra time can, and occasionally do, eliminate this blurriness, but generally it became a mark of ikat’s aesthetic quality.
An artisan has more planning to do, for the ikat can be made by tinting a pattern on the thread of the warp alone, or only a weft, and alternatively, on both warp and weft in which case it will become ‘double ikat’.
Back-strap or body tension loom. This is one of the earliest loom types, once common throughout the Indonesian Archipelago. This loom takes its name from a back-strap by which weaver’s body holds the warp threads in place and adjusts their tension. The loom is made of two bars with a back-strap passed around the weaver’s back and secured to the breast beam. The weaver controls the tension of the warp thread by leaning forward or back. These types of looms were easy and cheap to make and did not take up much space for storage.
Shaft loom or frame loom. This non-mechanical loom consists of a wooden box-like frame with a flat warp beam slotted into a pair of supports, suspended from a cross-bar. The frame loom allows tension of the warp thread to be regulated by the beams, without a need for a back-strap. This loom became increasingly popular during the colonial period in Indonesia and slowly replaced the traditional back-strap loom. It allows textiles to still be produced by hand, but at a much faster rate and so they are favoured by weavers who make the ikat for the market. Shaft looms also allow for different types of textiles to be created. For example skirts no longer needed to be produced as two panels and sewn together, but could be made as a single piece. Although the shaft loom became more widespread in Indonesia, cloths for ritual or ceremonial use are still made using the traditional back-strap loom.
Read about Ikat design
Explanations:
Ikat – the word, borrowed from the Indonesian language, describes the method of weaving that uses dyed threads to produce coloured patterns, as well as the type of fabric made in this process.
Warp is the set of threads running lengthwise in the loom (or vertical threads).
Weft is the set of threads that are woven across the loom (or horizontal threads).